.png)
Excellence in innovation 2018
Business Person of the Year 2018
Young Business Personality of the Year 2017


Client - Terumo BCT
Challenges for client - Broken production line part, machine down time, production down time, part obsolete, Teflon part with threads
Industry - Global leader in Blood management
.png)
Terumo BCT is a Global leader in Blood management, blood safety, therapeutic apheresis, cell therapy and cell collection. We were approached by one of their systems engineers regarding a part that had broken on one of their production line machines that managed Polyfusors. They could not source this part and needed an alternative. We got the part off them, reverse engineered it through CAD software and provided them with a quantity of 3D Printed replacements. We used PTFE, as this material met the requirements of the part. The part in question was made from Teflon so the replacement part had to have similar characteristics.
Solution and Result
By reverse engineering the Obsolete component and modelling in CAD, we could then 3D print a replacement. We used a material that was a suitable replacement for Teflon, offering similar characteristics which met the requirements of the client. The results for the client were reduced machine and production down time, a replacement part, spares and little effect on their personnel resources.
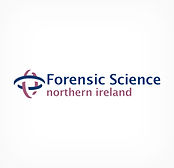
Client - Forensic Science NI
Challenges for client - Centrifuge insert, lack of stock, needed additional inserts to increase efficiency within the toxicology lab testing, difficult to source and machine material.
Industry - Forensics
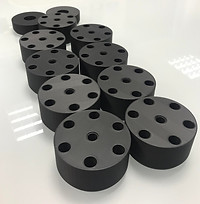
Operations in the field of forensics can often involve materials and components that are bespoke. For some time, FSNI needed additional centrifuge inserts that are used within the toxicology department. This meant they were not operating as efficiently as they could have been. FSNI approached us to see if we would have an alternative solution to their problem.
Solution and Result
We were able to offer our composite 3D Printing as a suitable alternative to the existing material, which was difficult to machine and hard to source. The part was then reverse engineered using the existing one, while our client waited at our offices. We supplied them with a quantity of the parts as well as different variants. For the client, they now are able to operate more efficiently and solved a long standing issue.
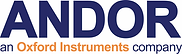
Client - Andor Technology
Challenges for client - Sourcing CNC aluminium alternatives for Jigs used on the production line and end use parts
Industry - High Technology
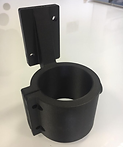.png)
Andor Technology is a golbal leader in the production of high value scientific imaging cameras. As an always developing business with new products a regular occurrence, there is a need for new production jigs. The mechanical engineering team, and in other instances their process engineers, reached out to us about the suitability of our 3D composite printing as an alternative to CNC machined aluminium.
Solution and Result
We recommended using Onyx, printed on our Markforged machine as the final printed product offers high strength, durability, accuracy and good aesthetics. We continue to work with Andor supplying them with Jigs as well as 3D Printed end use parts. These printed parts have been used in Andors end use, high value camera range.

Client - Wigglypeg
Challenges for client - Wanted mechanical design help to develop new versions of their existing innovative product
Industry - Consumer product
The Inventor of the Wigglypeg, a durable and easy to use clothes peg, approached us with his ideas for new developments of their existing product as he wishes to expand into new markets.
Solution and Result
We met with the client and he showed us the design ideas he was hoping to achieve. We advised him on what services we felt would benefit him, design and 3D Printed samples. Using CAD, we modeled his new design idea, liasing with the client throughout to ensure we were matching his requirements and vision for the new product. We then provided him with 3D Prints, in onyx, of the new designs. In addition to these, he now had CAD files that he can take to mass manufacturers for quotation.

Client - TeamGB Boccia Paralympian
Challenges for client - Wanted mechanical design help to develop a product that would assist her and others to hold accessories while in their wheelchair.
Industry - Bespoke product

The client had an idea for a new product that would allow her to hold accessories in front of her while in her wheelchair. She felt this product has commercial potential.
Solution and Result
After discussing the clients requirements, we first developed some concept designs. Once approved, we progressed to CAD modeling of the chosen design. The model was then 3D Printed on our Markforged machine. The end product also used aluminium, which we combined with the 3D Printed element. The end product was a great success and functioned as intended giving the client the ability to secure accessories in front of her when in her wheelchair.